What Is Condition Monitoring And How Does Internet Of Things Improve It?
Condition monitoring is a relatively new approach to equipment maintenance. To detect technical issues with a particular aspect of a machine’s functionality, technicians need to have precise measuring devices and powerful means to store data. With a powerful condition monitoring system, gathering and analyzing massive amounts of information has become much easier.
According to a report from Markets and Markets, the market for condition monitoring was valued at 2.21 billion dollars in 2017. This number is predicted to grow at least to 3.5 billion in 2024. With such growth, there is no wonder that global governments and industrial leaders recognize the importance of condition monitoring and create initiatives and funds for such systems.
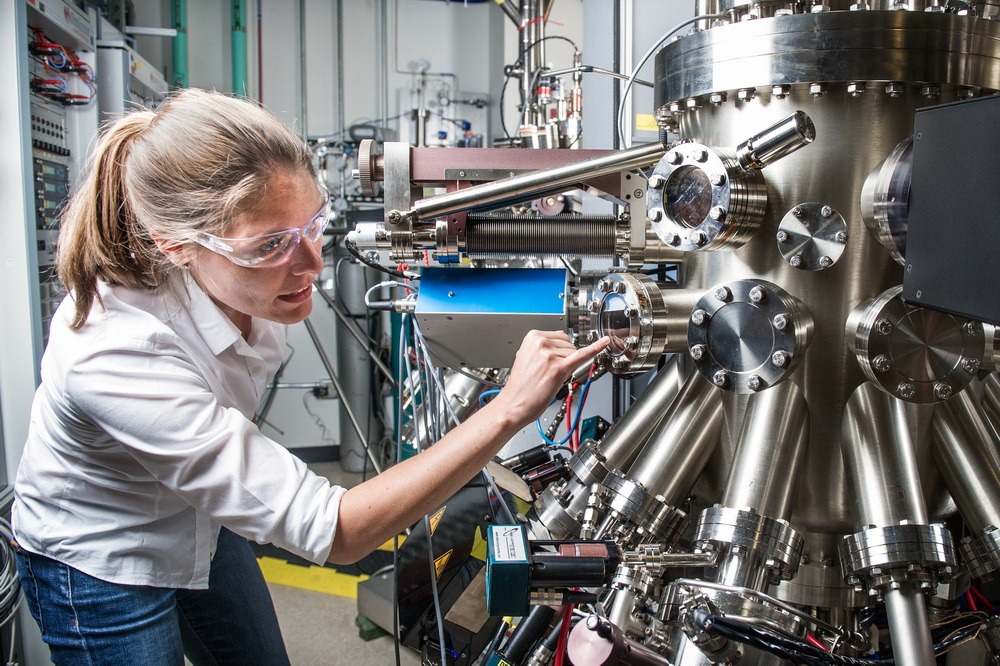
Table of Contents
- What Is Condition Monitoring?
- What Industries Can Use A Condition Monitoring System?
- Types of Conditions Monitoring
- Condition Monitoring Techniques
- Benefits of Condition Monitoring Systems
- Role of IoT in Conditions Monitoring
- Condition Monitoring Solutions with Digiteum
What Is Condition Monitoring?
Condition monitoring is the process of controlling specific parameters of a machine to detect possible technical issues before it leads to noticeable damage. By tracking the temperature or vibration of machine details, it’s possible to detect a potential technology failure and repair it immediately. The data is communicated via devices connected by the Internet of Things.
Typically, IoT monitoring is applied to the most fragile components of the machinery — rotating parts, combustion equipment, engines, and pumps. These are typically the dynamic elements of the construction that are predisposed to wear down faster. Often, these are also the key parts of the machinery, on which the functionality of the hardware depends the most — damaging them would have long-term consequences.
What Industries Can Use A Condition Monitoring System?
Condition monitoring service is useful in all fields that interact with machines and technology. It’s often used in innovative fields where the cost of repair would be unreasonably high due to the innovative nature of the machinery. In any industry, where dealing with damage is more expensive than investing in predicting it, conditions monitoring is a must. Let’s see some examples.
Green energy
International organizations are actively investing in moving away from fossil fuel energy production and focus on developing sustainable and potentially cheaper solutions. Solar, hydroelectric, and wind energy machinery is still considered an innovation, so replacing a broken part is rather complicated — the engineering team would have to rebuild a piece of complex technology.
Wind turbines, for instance, require especially precise condition monitoring during the winter season — that’s when the machines produce two-thirds of yearly energy. A failure of the turbine during this active season would mean huge economic losses. Additionally, repairing a turbine during winter is harder due to weather and temperature. The European Union recognized these issues and funded IoT condition monitoring software that detects the fluctuations in wind turbines.
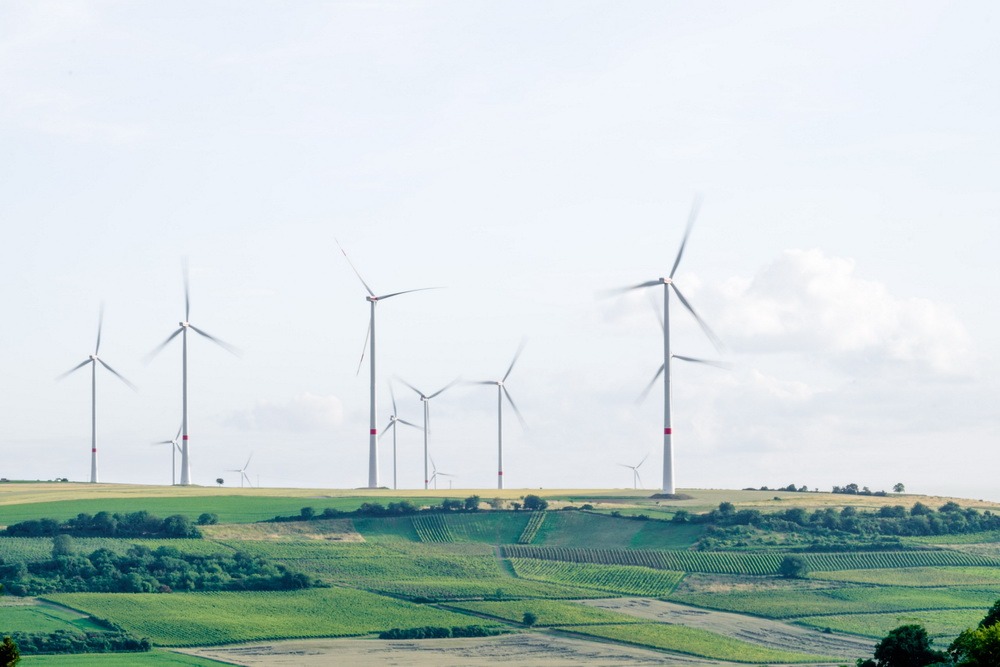
Food Production
Food products are sensitive to their storage conditions — the maintenance cost comprises 20% of overall production expenses. Even little variations of humidity temperature, hygiene, or vibration can increase the risk of food contamination or lead to product waste.
Oil Companies
Technical issues with oil and gas production and refining equimplemt result in huge environmental and financial damage. This is why using IoT sensors for oil and gas machinery and integrating predictive maintenance is a must in this industry. Engineers have to check the reliability of generators, compressors, turbines, and motors and analyze their performance with smart analytics. Smart condition monitoring solutions can predict these challenges and offer ways of optimization.
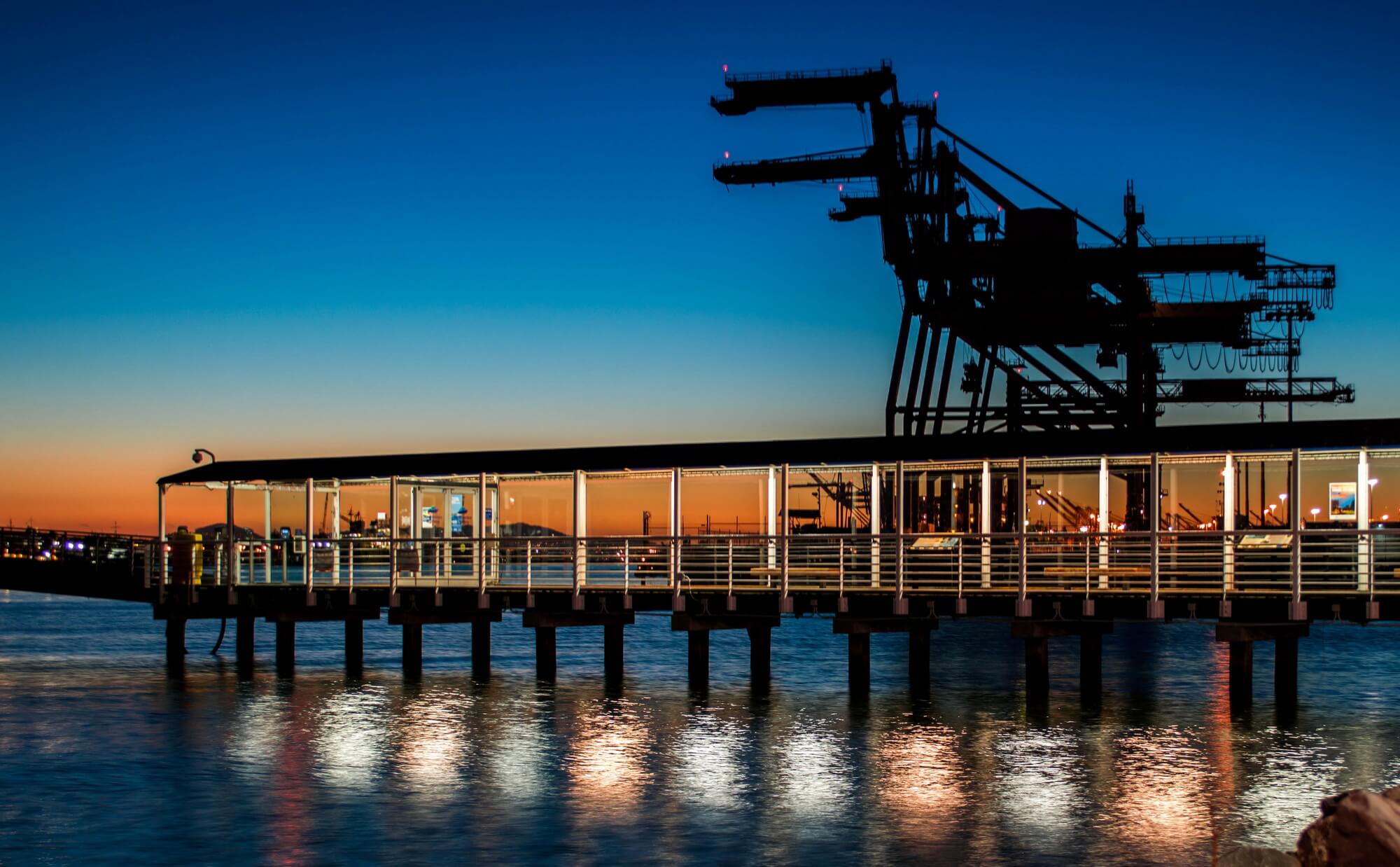
Military
Repairing damaged military equipment is expensive and potentially dangerous. If an armored vehicle fails during the operation, the financial and human cost of this error can be of a catastrophic extent. To prevent high-performance equipment from unexpected failures, military engineers monitor the machinery and invest in automated technology that can analyze the conditions of the machinery parts remotely during an operation.
Transport
Accidents, delays, and unfavorable weather conditions can inflict huge damage on transportation and bring associated costs. Condition systems can track the variations of the machine’s performance in unexpected circumstances and alert providers about possible damages. Moreover, they can use weather forecasts and predictive analytics to foresee possible surprises and assist the teams in preparing the vehicles.
Read: Smart city ideas using IoT in infrastructure, transportation, sustainability and security
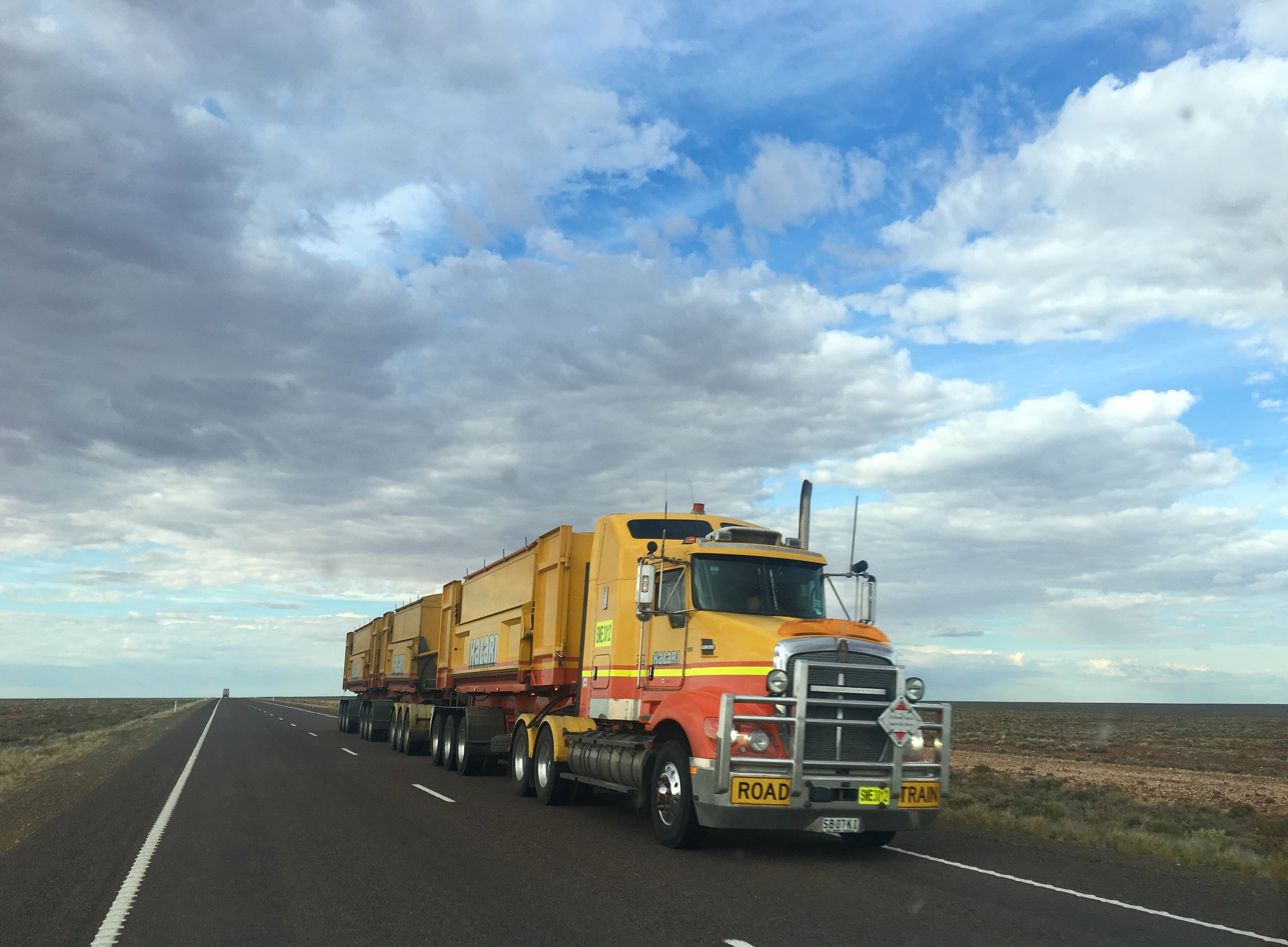
Types of Conditions Monitoring
Condition Monitoring is a versatile practice, used in different industries for various types of machines. To satisfy the dynamic needs of industrial companies, teams have to apply different kinds of condition monitoring. Let’s take a closer look at the five of the most common methods where IoT is used most frequently.
1. Route-based monitoring
This is an immediate monitoring activity where a technician uses a handheld device to measure a particular condition. For instance, if a worker uses an IoT handheld temperature measuring device to get data on a refrigerator’s performance, that’s an example of route-based monitoring.
This on-the-go method is used for rough estimates, as the data isn’t always absolutely precise. It’s used to identify problematic areas and determine where to proceed with a deeper analysis. If route-based monitoring doesn’t detect any issues or caused suspicions, more advanced methods are hardly required.
2. Portable machine diagnostics
Portable monitoring requires portable devices, possibly with Internet of Things technology, that make precise measurements on system conditions and performance. These instruments are more reliable than handheld devices, and due to their mobility, they can be used on multiple pieces of machinery without being attached to a specific detail of a system.
3. Factory assurance test
These measurements are performed on a ready product that fully underwent its production cycle. The product is evaluated by key design specifications and possible failure scenarios. The objectives of this monitoring are to determine if the end product responds to the standards and identify potential risks.
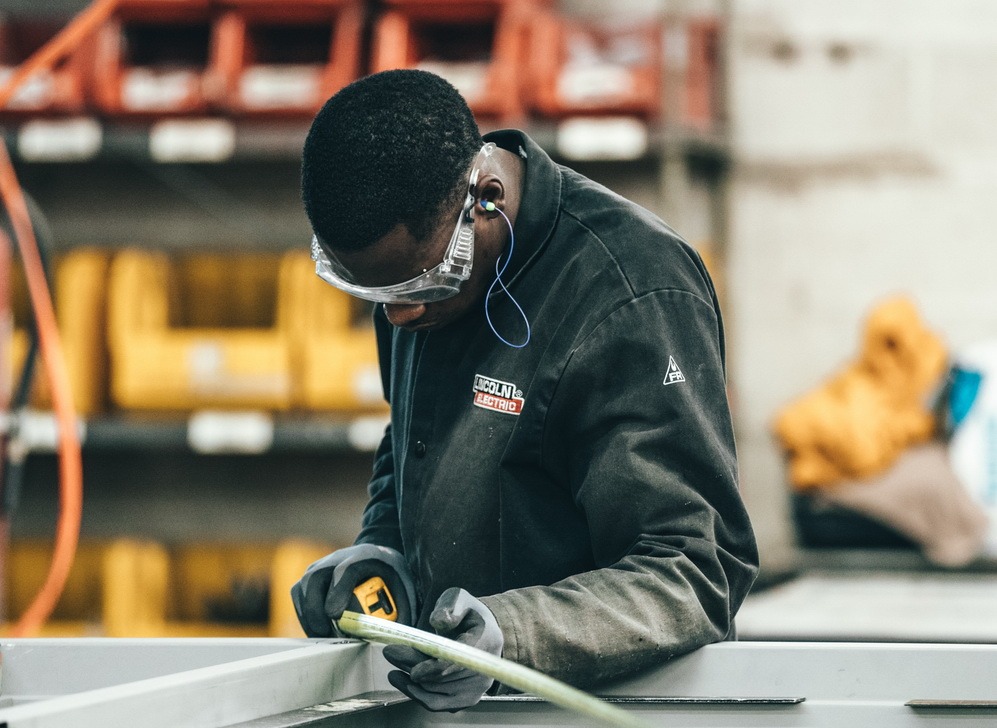
4. Online machine monitoring
Online machine monitoring relies on real-time data transmission from IoT sensors that measures equipment performance in their active state. When the device is running, the measuring instrument embedded in the system transmits the information to the server for further analysis.
Read: Top IoT hardware platforms for building connected systems
5. Online machine protection
Online machine protection is similar to online machine monitoring in its execution — the measurement instrument is attached to the equipment and records its performance data in the active state while transmitting it to the server in real-time. However, unlike general monitoring, protection is focused on turning off the equipment if any damage or abnormality is detected. The devices are equipped with limit settings that set thresholds for particular characteristics.
Condition Monitoring Techniques
The list of CM methods is extensive, due to the versatility of the industries in which it’s applied. Various fields make use of different instruments and work with various settings, and these needs require specific approaches. Still, these techniques can be generalized into four common types.
Vibration monitoring and analysis
This is a type of monitoring that’s usually applied to rotating machinery. Technicians place electric transducers-sensors (they can be connected to the IoT device) and check a part’s velocity, acceleration, or displacement by analyzing electrical inputs and outputs.
After the vibration data is successfully collected, the software analyzes the vibration velocity and indicates the condition of the detail. Further, the team may perform frequency analysis and compare the spectrum with the data from a well-functioning machine.
Ultimately, the software or team makes a comparative analysis and determines how much vibration can detail or a machine undergo without being damaged. The vibration threshold is set — if the levels of vibrations are higher than allowed, the equipment is either automatically shut down or switched to a less intense working mode.
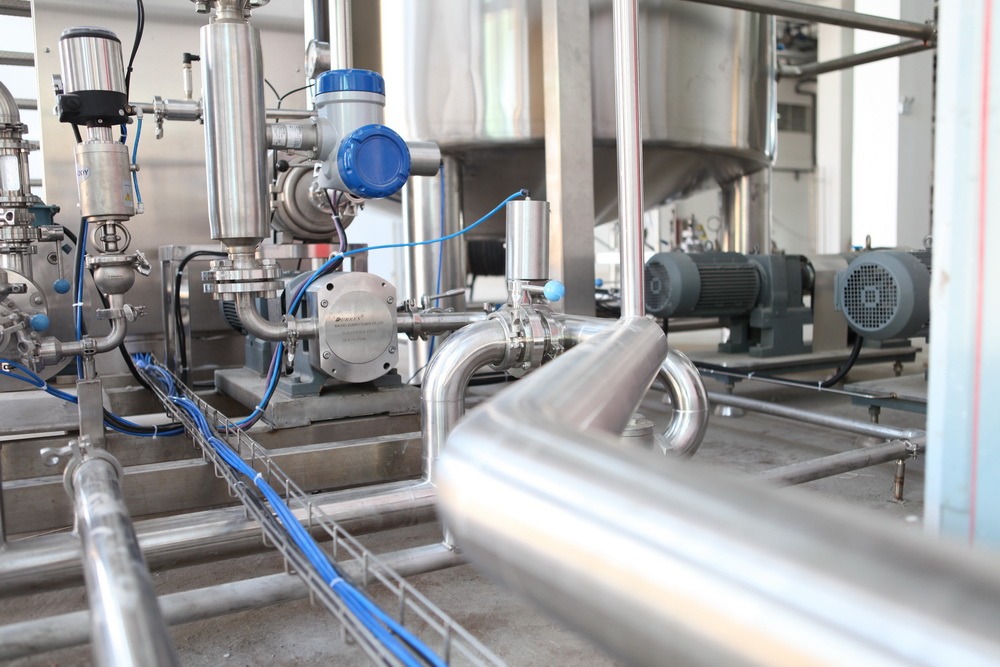
Debris monitoring and analysis
The debris monitoring is usually used in machinery that deals with oil and fluid substances. There are several techniques for performing such an analysis. The oldest one requires the use of a magnetic plug for ferromagnetic debris detection. The magnet collects the debris particle, and the team can collect them from the plug and examine them carefully.
The debris analysis can also be performed with electrical methods. Metallic particles indicate the number of particles in the fluid by attracting the debris to the electrodes. The electrode is taken out and the collected debris is analyzed. Debris can also be analyzed with filters and cartridges. As soon as the filter becomes clogged with debris, the team receives an alert.
All these methods can be automated by using IoT sensors. Magnets, filters, and electrodes can be connected to the IoT device and transmit data in real-time, alerting the team on when it’s time to take the detectors out and proceed with the analysis.
Thermal imaging
If the equipment emits infrared radiation, its quantity and quality can be analyzed to provide information on the overall machine’s productivity. At first, it’s necessary to examine the infrared energy under normal conditions from a healthy machine. Secondly, the team runs the machine in stressful conditions, trying to predict its behavior in unexpected situations.
The method determines hot and cold spots. Areas that are too heated are likely to go out of order faster — it may indicate uneven heat distribution. The cold parts, on the other hand, can be affected by water — it’s necessary to check whether there is a leakage.
Acoustic emission (AE)
This method is used to analyze the moving parts of the equipment to see if there is any unnecessary friction between the details. If the moving surfaces enter unnecessary contact, it will lead to lost energy and cause the details to wear out. Acoustic emission directs the waves that appear from contact with a surface.
Acoustic emission is a technique of online machine monitoring — it requires the machine to be in the active state and transmits data to a server in real-time. It’s used for rotating and non-rotating surfaces and detects the machine’s levels of activity. The most active areas are the most vulnerable ones. The team detects these zones and knows what issues to prioritize.
Benefits of Condition Monitoring Systems
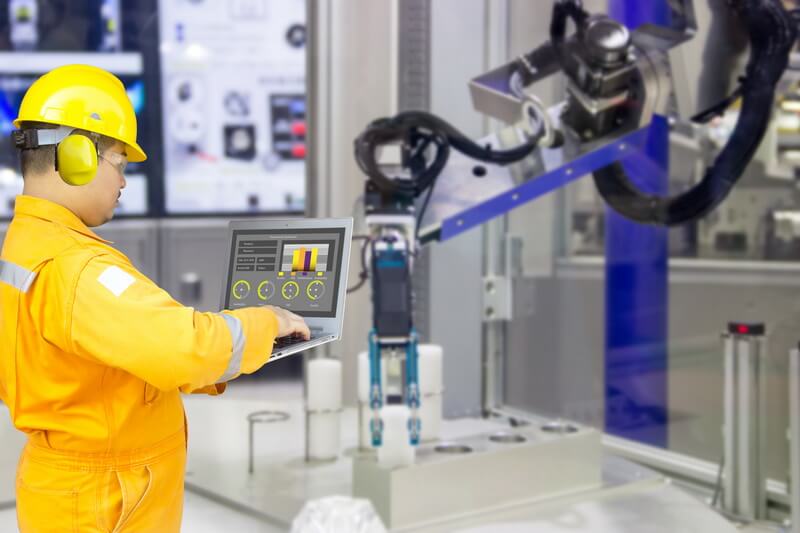
Condition Monitoring allows avoiding potential equipment damage by analyzing the most vulnerable areas, allowing teams to tend to these issues in time. This has a huge impact on productivity and end-product quality.
Decreasing maintenance expenses
Facing system damage is expensive in many industries because the productivity of the entire unit or factory can end up jeopardized. Detecting internal machine issues plays a key part in preventing this damage. Condition monitoring eradicates the approach of fixing things as they break, and re-directs efforts to predictive maintenance based on smart analytics. Teams can deal with damage on their terms, minimizing the losses and planning the repair work.
Maximizing production output
Faulty machinery reduces the team’s productivity, preventing employees from fulfilling their work tasks. This stalls the production progress and requires the companies to pay for unproductive hours — since workers can’t necessarily be held responsible for these technical issues. IoT based condition monitoring helps to avoid these work interruptions and increases production volumes.
Prolonging the lifespan of the equipment
It’s important to note that machines are rarely broken fully — usually, there are a lot of well-functioning parts. It would be a waste to replace an entire asset when in reality, only 2-3 details need to be patched up. Condition monitoring allows us to fix broken machinery instead of replacing it. Business owners don’t have to buy an entirely new machine — instead, they identify the problematic areas in the existing ones and tend to their issues one by one.
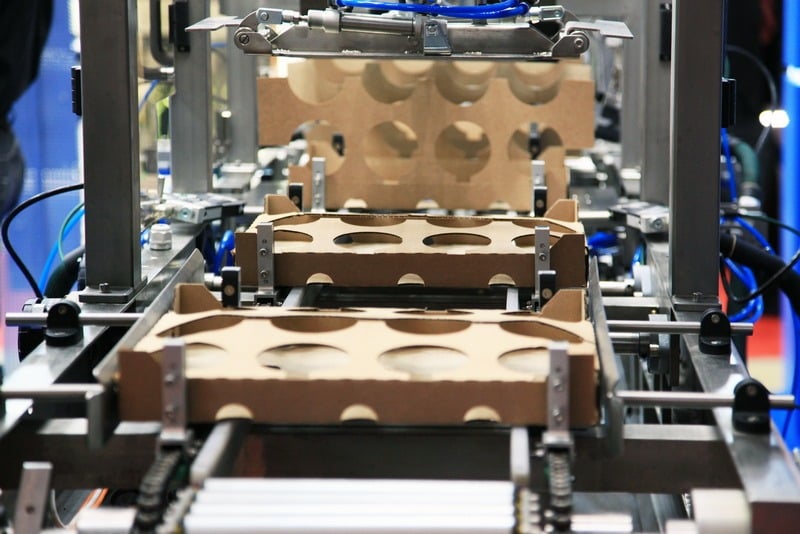
Planning smart maintenance
Owners, engineers, and technicians can maximize their productivity by synchronizing their maintenance schedules. Instead of working chaotically to repair an urgently broken machine, they can detect the damage beforehand and allocate work in a smart way that doesn’t prohibit the team from tending to other priorities.
Preserving safety
Industrial, transport, military, and other accidents harm not only people who are directly related to the equipment, but also habitants of nearby territories. Also, grave malfunctions usually lead to serious environmental disasters. One such incident can lead to serious legal and financial consequences, or even stop the production altogether. Condition monitoring allows detecting potentially dangerous pieces of machinery before they cause a catastrophe.
Role of IoT in Conditions Monitoring
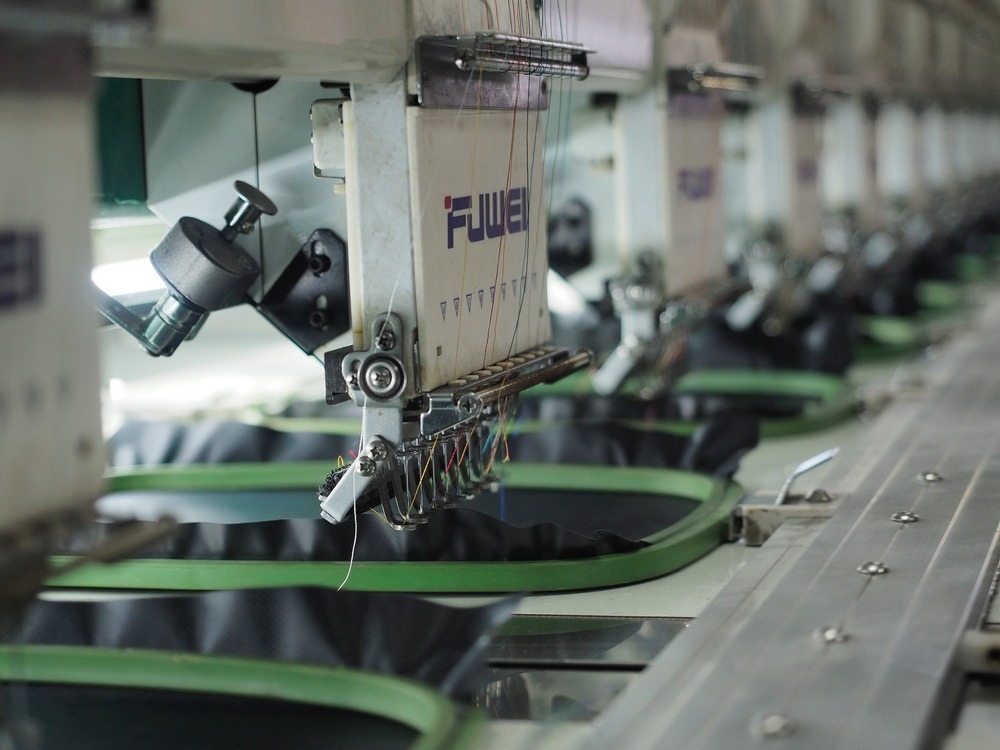
The Internet of Things uses sensors, trackers and communicating condition data from connected devices. The team can access the data from their laptops and smartphones anytime and anywhere. Whenever there is a crisis, a responsible person will be immediately alerted. Let’s see how IoT for condition monitoring contributes to efficient maintenance.
Cloud computing
Industrial objects generate a lot of information and storing them on hard drives is expensive — the physical servers take a lot of space which requires investments. IoT Cloud computing allows storing the data on remote servers, located all over the world. Employees access this data via secured personal accounts. The company doesn’t have to worry about protecting their physical local drives, this is a responsibility of a Cloud storage provider.
Machine learning
IoT platforms are used to collect and process sensor data, and apply analytics and machine learning algorithms to make sense of this data. For instance, a device can collect the vibration data from a drilling machine. The algorithms will go through this information and detect broken drills. For an employee, going through these amounts of data is nearly impossible.
Automated schedules
Teams can schedule condition monitoring from their smartphones, determining when a sensor should start transmitting data. They can view, manage, and cancel the process from smartphones or laptops while not being physically present at the check site.
Remote equipment
In certain industries, like oil production or military, the equipment is often away from the production and maintenance location. IoT sensors can transmit data from the remote machinery and send it to the centralized server. An armored vehicle can be located in Africa, but the team in the US will receive updates on its performance in real-time. If there are issues, they can shut down the equipment or switch its operating mode.
Condition Monitoring Solutions in Digiteum
Our IoT software development team has the skillset to design and build condition monitoring applications to industrial and agricultural markets. Using our industry, technology and business expertise, we help companies across the globe optimize and automate their processes and get valuable insights that improve their decision-making.
If you are working on an IoT system for condition monitoring and looking for a skilled IoT software development service provider, get in touch with Digiteum. Take a look at our related projects for more information.